Cómo reducir pérdidas en el transporte de mercancía ocasionada por daños en el embalaje
En un contexto logístico más globalizado y regulado, reducir daños y pérdidas de la mercancía durante el transporte es ya una asignatura obligatoria. Con el aumento de exigencias internacionales y nuevas normativas en la cadena de suministro, garantizar la integridad de los productos durante su transporte es el objetivo de los sistemas de embalaje final. Pero ¿qué porcentaje de pérdidas se ocasiona por problemas o fallos del propio embalaje? Aunque la maquinaria de embalaje tenga el objetivo de asegurar la carga, a menudo pueden ocasionar fallos que no solo resulten en productos dañados, sino en otros costes adicionales significativos para la empresa.
En este artículo, exploraremos cómo abordar este desafío logístico, analizando las pérdidas de coste más comunes por fallos en el embalaje y cómo reducirlas de manera efectiva.
Pérdidas más comunes ocasionadas por fallos en el embalaje
A continuación repasamos todos los aspectos donde la empresa podría perder rentabilidad debido a problemas con el embalaje.
1. Producto dañado o con desperfectos
Una de las pérdidas más evidentes y costosas es el daño que pueden sufrir los productos en el transporte. Aquí no sólo hablamos de producto estropeado o roto directamente por falta de estabilidad (deslizamiento de carga, vertido o caídas de producto, golpes en el envase, etc) si no también de producto que ha sido dañado por falta de protección contra agentes externos (lluvia o nieve durante el trayecto, humedad, etc).
¿Qué cantidad de palets quedan inservibles a final de mes? ¿Cuántas unidades de producto sufren desperfectos durante su manipulación y transporte? La empresa debe analizar estos datos para determinar el rendimiento del sistema de embalaje o procesos logísticos.
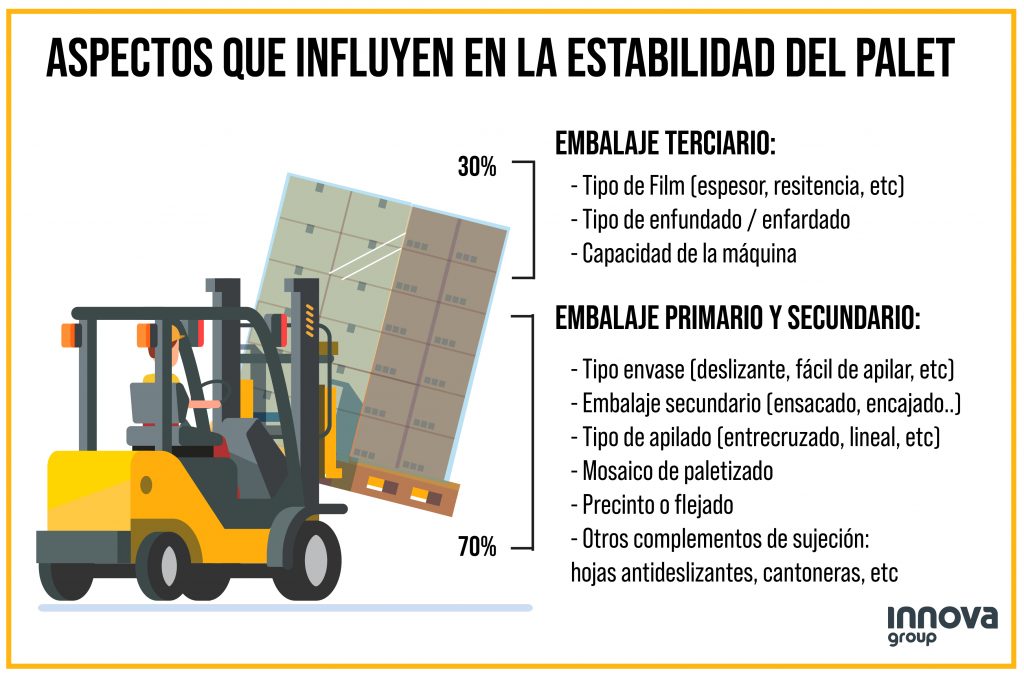
2. Costes adicionales para el reenvío de producto
Un aspecto adicional que con frecuencia se pasa por alto al calcular las pérdidas en rentabilidad ocasionadas por productos dañados son los costes suplementarios asociados al reenvío de los productos. Por lo general, estas pérdidas están vinculadas a un pedido que debe ser completado y enviado nuevamente.
Este proceso conlleva una serie de gastos como costes de envío adicionales, mano de obra y el tiempo dedicado a la reorganización y reembalaje de los productos dañados. El reenvío también puede implicar una demora en la entrega al cliente, lo que podría afectar la satisfacción del cliente y generar un coste indirecto en forma de entregas canceladas o disminución de pedidos en el futuro.
3. Material de embalaje dañado
El embalaje en sí mismo puede sufrir daños, como el film estirable o el fleje, lo que agrega costes por el material de embalaje perdido que no ha cumplido su función. Aquí cabe plantear: ¿Cuánto film extra se ha tenido que utilizar en embalar el producto de nuevo para su envío?
En el caso de sistemas de embalaje automatizados puede que el sobrecoste de volver a embalar el producto no sea elevado (ya que dichos sistemas están diseñados para el consumo mínimo de film/fleje), pero a menudo en procesos manuales o semiautomáticos se utilizan otros tipos de embalaje de valor superior cómo por ejemplo soportes o escuadras de madera, cintas o correas de amarre, cantoneras de metal, etc.
4. Costes adicionales de mano de obra y productividad
Los productos dañados requieren recursos y tiempo adicional para ser manipulados, reempaquetados o reparados. De nuevo, en procesos de final de línea automatizados puede no ocasione un coste elevado en pérdidas puntuales, pero en finales semiautomáticos o bien automatizados con sistemas de embalaje antiguos, puede que el coste de personal y productividad de reponer y reembalar sea mucho mayor.
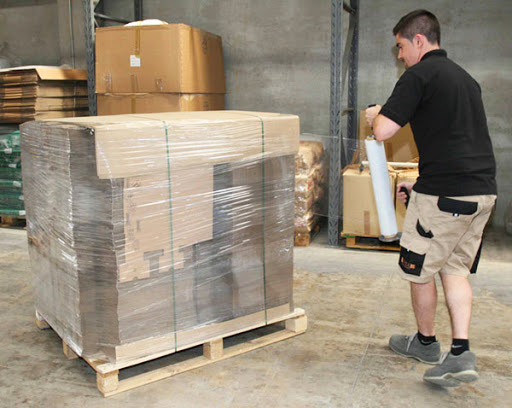
En este punto será vital revisar todo el proceso de embalaje para ver que puntos se deben optimizar (si es el sistema de embalaje o el propio proceso de embalado).
5. Aumento del coste del seguro de envío para los productos
Otro coste secundario es el de un incremento en el seguro de los envíos. Si las pérdidas en el transporte son frecuentes, es probable que los costes de seguro en los envíos de mercancía también aumenten. A medida que las reclamaciones por pérdidas se vuelven habituales, las compañías de seguros pueden considerar que la empresa representa un riesgo más alto.
6. Entregas canceladas y clientes insatisfechos
Más allá de los costes tangibles que implica el daño en los productos, es importante considerar el impacto de la insatisfacción del cliente y las entregas canceladas en la reputación de la empresa y en sus ventas a futuro. Cuando un cliente recibe un producto dañado o experimenta una entrega retrasada debido a incidentes durante el transporte, su nivel de satisfacción se ve comprometido.
Por lo tanto, reducir al máximo las pérdidas durante el transporte no solo se traduce en ahorros inmediatos y eficiencia operativa, sino que también juega un papel fundamental en la preservación de la imagen de la empresa y en su capacidad para mantener y expandir su base de clientes a lo largo del tiempo.
Cómo calcular los costes de pérdidas en los envíos
Calcular los costes reales de pérdidas en los envíos es esencial para comprender el impacto financiero y tomar medidas efectivas para reducirlos. Esto implica tener en ceunta todos los costes directos e indirectos asociados con los productos dañados, como los mencionados anteriormente:
- Coste del producto/s dañados
- Coste del transporte afectado y el segundo transporte de reenvío del producto
- Coste de reembalar y preparar la mercancía de nuevo: consumibles y sistemas de embalaje usado, tiempo de productividad de la línea
- Coste de mano de obra implicada en el retrabajo
- Otros costes secundarios (incremento de seguros, cancelaciones de pedidos, etc)
¿Cómo reducir las pérdidas con los sistemas embalaje?
La clave reside en mejorar el proceso de embalaje para evitar que éste sea el causante de daños y pérdidas de mercancía. Ya sea con la maquinaria existente o renovando los sistemas de embalaje, es importante medir, evaluar y corregir.
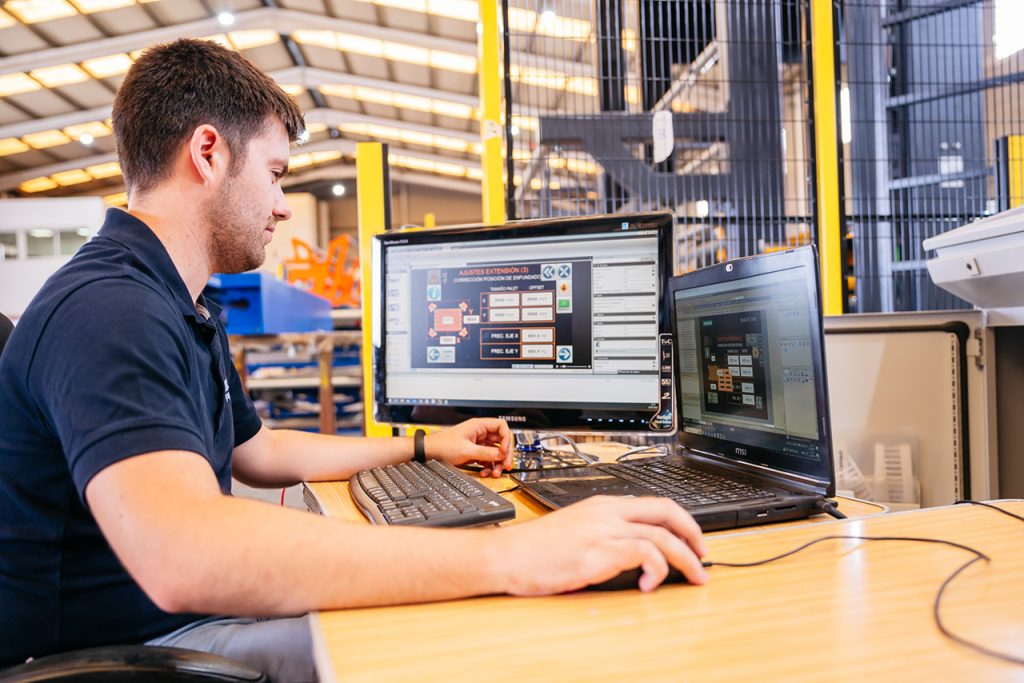
Evaluar y optimizar la maquinaria de embalaje existente
El primer paso es analizar el rendimiento del proceso de embalaje y sistemas usados en el momento, para detectar donde está fallando el objetivo de asegurar y proteger los palets. Así pues analizaremos varios aspectos:
1. Evaluación del proceso de embalaje:
Comenzamos por evaluar la eficacia de los sistemas de embalaje en uso: tanto si son semiautomáticos como automáticos, hay que realizar mantenimiento y limpieza, actualización de programación, ajustes de embalaje, etc.
2. Análisis de la sujeción de la carga y los consumibles utilizados:
En este punto podemos evaluar que la tensión (ya sea del fleje o del film usado) sea la correcta. También cabe analizar que los consumibles que estamos usando sea los adecuados para el producto que estamos embalando. Por ejemplo: ¿es necesario flejar si ya enfardamos el producto? ¿necesitamos mayor protección en caso de solo usar envolvedora?
Para este punto te recomendamos leer el siguiente artículo en que abordamos tipos de embalaje según los objetivos de protección:
3. Determinar especificaciones de fleje o film adecuadas para el producto:
En línea del anterior punto también hay que escoger las especificaciones del consumible según las necesidades específicas de embalaje de cada producto. En este punto hablamos de características del propio film (si es estirable, con preestiro o sin), gramaje, componente reciclado, etc
4. Mantenimiento preventivo regular de los sistemas de embalaje: Otro punto crítico es realizar un mantenimiento preventivo programado de las máquinas y equipos de embalaje para garantizar su buen funcionamiento y prolongar su vida útil. Parece obvio, pero 2 de 4 fallos en el proceso de embalaje se ocasiona por una máquina sin mantenimiento, ni engrasado habitual.
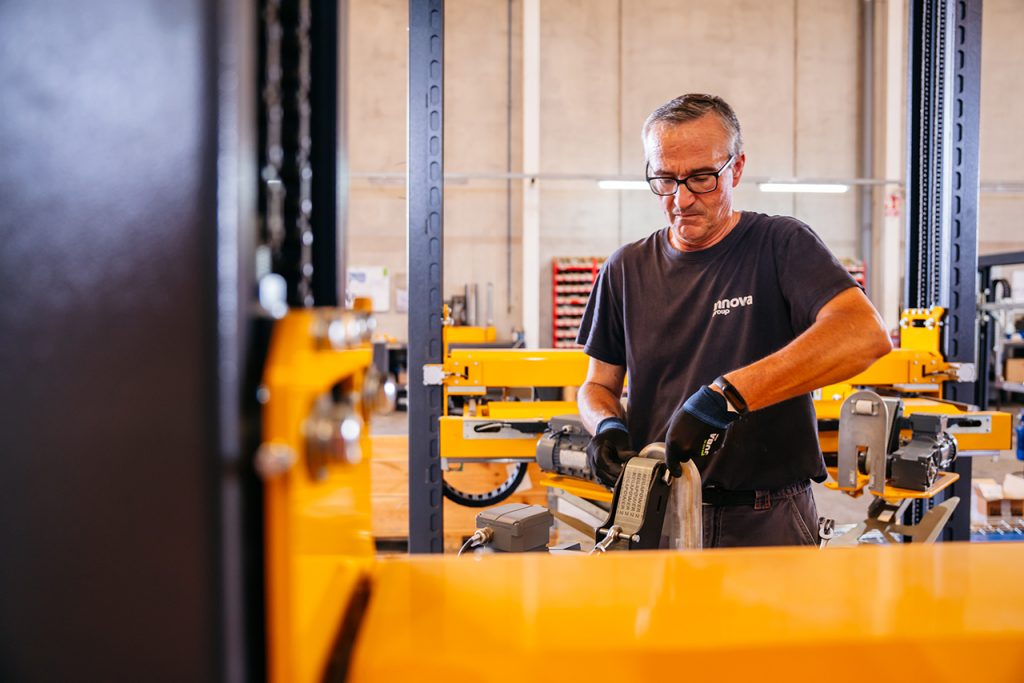
5. Seguimiento y análisis de datos del final de línea:
Además de las medidas mencionadas, otro aspecto esencial es la implementación de sistemas de seguimiento y análisis de datos. Estos sistemas permiten monitorear el desempeño del embalaje y recopilar información valiosa sobre los incidentes de daños durante el transporte.
Esta acción nos permitirá mantener un registro detallado de todos los problemas durante el transporte, identificar patrones y tendencias, y utilizar los datos recopilados para implementar mejoras continuas en el proceso de embalaje y transporte.
Reducir pérdidas con nuevos sistema de embalaje
En el punto en que los procesos del final de línea y sistemas de embalaje se han quedado obsoletos y/o ocasionan más problemas que resuelven es sin duda el momento de cambiar y actualizar los sistemas de embalaje. El paso hacia la automatización total y/o renovación de sistemas más avanzados es difícil de tomar pero la inversión se amortiza rápidamente ya que ayuda a prevenir daños y pérdidas desde el principio.
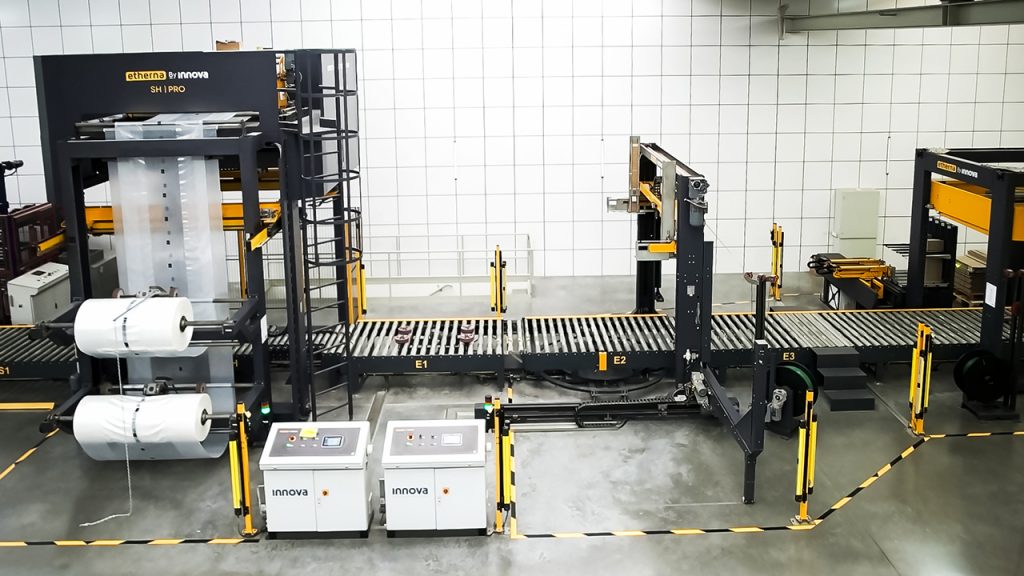
Ejemplos de sistemas de embalaje más modernos incluyen envolvedoras de alto rendimiento, cómo las envolvedoras de anillo automáticas, y sistemas de enfundado Stretch Hood, que ofrecen una mayor protección y eficiencia en el embalaje. En Innova, con más de 20 años como fabricantes de equipos de final de línea te podemos asesorar en el proceso de renovación de tus sistemas de embalaje.
En resumen, la reducción de pérdidas en el transporte de mercancía debido a daños en el embalaje es esencial para optimizar la cadena de suministro y reducir costes innecesarios. Evaluar y mejorar el proceso de embalaje, así como invertir en maquinaria de embalaje de última generación y sistemas de seguimiento de datos, son pasos fundamentales para lograr este objetivo y mantener a los clientes satisfechos. No dudes a contactar con nosotros para asesoramiento en cómo optimizar tu procesos de embalaje, estaremos encantados de atenderte.
¿Te gustan nuestros posts técnicos? Suscríbete a nuestra Newsletter mensual de notícias y tendencias de packaging y logística.
SUSCRIBIRSE AL BLOG: