Claves de un plan de mantenimiento inteligente (o cómo alargar la vida de tus sistemas de embalaje)
El mantenimiento es una de las piezas principales que garantiza el funcionamiento de la maquinaria. Pero ¿cómo aplicar el mantenimiento para mejorar aun más el rendimiento de ésta y extender la vida de la máquina? A menudo vemos fábricas en las que sistemas de embalaje automático con un mantenimiento pobre e ineficiente ralentizan todo el proceso y los resultados, además de ofrecer un aspecto de instalación antigua aunque los equipos solo cuenten con unos años. Y al contrario, visitamos fábricas con máquinas de más de 15 años en las que los equipos funcionan como el primer día. ¿Cuál es el secreto?
En este artículo, cómo fabricantes de sistemas de embalaje con experiencia de casi 25 años de mantenimientos, desgranamos todos los aspectos del mantenimiento preventivo y cómo implementarlo para evitar la degradación y obsolescencia de tus equipos.
Sistemas de embalaje «cómo el primer día», con mantenimiento preventivo
El objetivo del mantenimiento preventivo es detectar y corregir cualquier posible problema antes de que provoque una falla en el equipo, reduciendo así el tiempo de inactividad y la necesidad de reparaciones costosas. Pero no sólo es una prevención de averías, si no que busca prolongar el ciclo de vida del equipo.
La implementación de un mantenimiento preventivo en maquinaria de embalaje, como las máquinas Stretch Hood, envolvedoras de palets y flejadoras de palets, presenta numerosos beneficios que impactan directamente en la eficiencia y productividad de las líneas de embalaje:
- Mayor fiabilidad de los equipos: Al realizar inspecciones y tareas de mantenimiento regulares, se pueden identificar y abordar problemas potenciales antes de que provoquen fallas. Esto ayuda a garantizar que los equipos operen a su máxima capacidad y a minimizar los tiempos de inactividad.
- Reducción del tiempo de inactividad: Al identificar y solucionar problemas antes de que causen una falla, se minimizan los tiempos de parada, manteniendo una producción sin interrupciones y evitando así pérdidas para la empresa.
- Incremento de la productividad: Cuando los equipos operan a su máxima capacidad, la productividad aumenta, lo que mejora la eficiencia y reduce la necesidad de horas extras o recursos adicionales.
- Extensión de la vida útil del equipo: Implementar un programa de mantenimiento preventivo en maquinaria de embalaje automático es una inversión inteligente para cualquier empresa que busque mejorar la fiabilidad de sus equipos, aumentar la productividad y reducir costes. Al inspeccionar y mantener los equipos regularmente, se garantiza que operen de manera segura y eficiente, y se alargue su ciclo vital.
- Reducción de costos de reparación y reemplazo: Identificar y solucionar problemas antes de que provoquen fallas permite reducir los costos de reparaciones y reemplazos a largo plazo.
- Cumplimiento de las normas de seguridad: Mantener los equipos en buen estado de funcionamiento también contribuye a cumplir con las normativas de seguridad, reduciendo el riesgo de accidentes e incidentes.
- Mantenimiento de la calidad del producto: Mantener los equipos en óptimas condiciones ayuda a garantizar que los productos cumplan con las expectativas del cliente y los estándares de la industria.
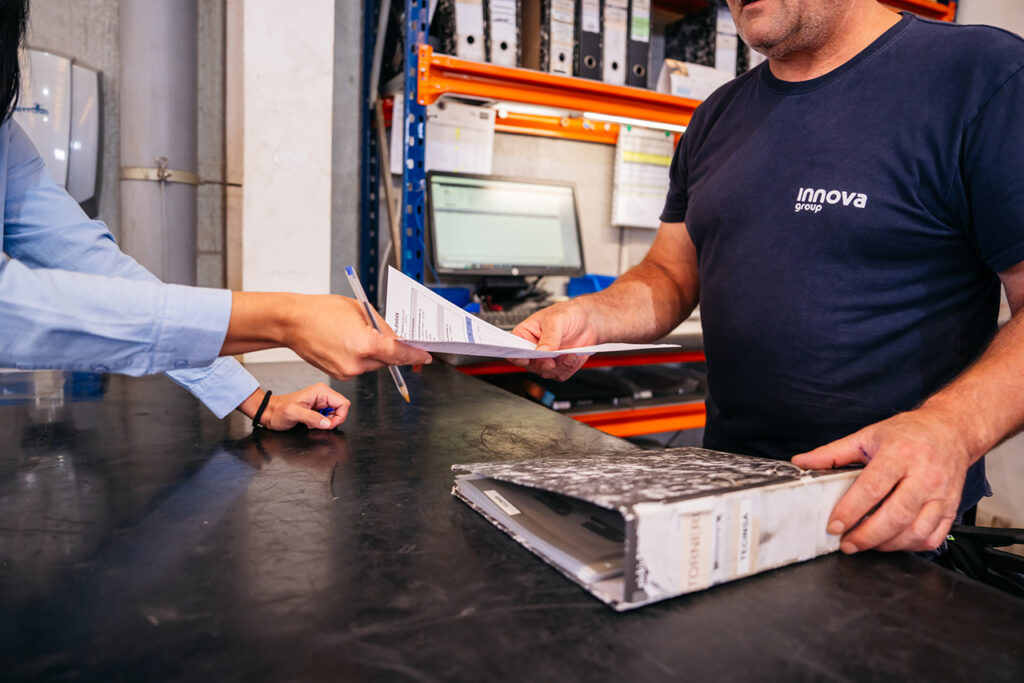
Sobre la eficiencia de una línea de embalaje, te recomendamos leer nuestro artículo dedicado a la medida del indicador OEE, sobre el rendimiento y eficiencia de los equipos:
¿Cómo implementar un programa de mantenimiento de sistemas de embalaje?
Aunque a menudo el plan de mantenimiento es responsabilidad del fabricante y recae sobre éste planificarlo, es importante que el cliente y usuario de los equipos conozca cómo se llevan a cabo estos planes para poder dar mejor seguimiento y exigencia de resultados.
Aspectos para implementar un plan de mantenimiento:
- Establecer una planificación temporal: La frecuencia del mantenimiento de los equipos de embalaje depende del tipo de equipo, su entorno de uso y nivel de utilización, pudiendo basarse en un cronograma fijo (semanal, mensual, trimestral o anual…) o en el uso real del equipo, monitoreando indicadores clave de rendimiento (KPIs). Mientras que el enfoque basado en el tiempo establece tareas regulares como inspección, limpieza, lubricación y reemplazo de partes, el enfoque basado en el uso permite optimizar los recursos al realizar el mantenimiento solo cuando es necesario, según los datos de operación del equipo.
- Definir el plan de mantenimiento: Especificar las tareas específicas que deben realizarse en cada etapa o intervalo del mantenimiento: limpieza, lubricación, ajustes, calibración, reemplazo de piezas, etc o bien en base a los resultados, tal y cómo comentamos.
- Adecuación del programa a las condiciones de fábrica: Las condiciones del entorno, como la humedad, la exposición al polvo o a productos químicos, pueden afectar la maquinaria de embalaje. Por lo tanto, es recomendable implementar programas específicos que consideren medidas adicionales, como el uso de recubrimientos protectores, sellos especiales, o materiales resistentes a la corrosión.
- Documentación y registros: Es necesario documentar todas las tareas de mantenimiento realizadas, incluyendo la fecha, hora y cualquier problema identificado o resuelto. Esta información es crucial para identificar patrones de fallas y evaluar la efectividad del programa de mantenimiento.
- Gestión del inventario de piezas: Mantener un inventario de piezas de repuesto y consumibles disponibles para que las tareas de mantenimiento puedan llevarse a cabo de forma rápida y eficiente, minimizando los tiempos de inactividad. Por ejemplo, en Innova nuestro servicio de repuestos se organiza mediante un almacén inteligente que permite mejorar la eficiencia tanto del servicio de soporte cómo el de mantenimiento.
- Reporting 4.0 y mantenimiento predictivo: Utilizar datos y tecnología 4.0 para monitorear el rendimiento y desgaste de los equipos y predecir cuándo será necesario realizar el mantenimiento.
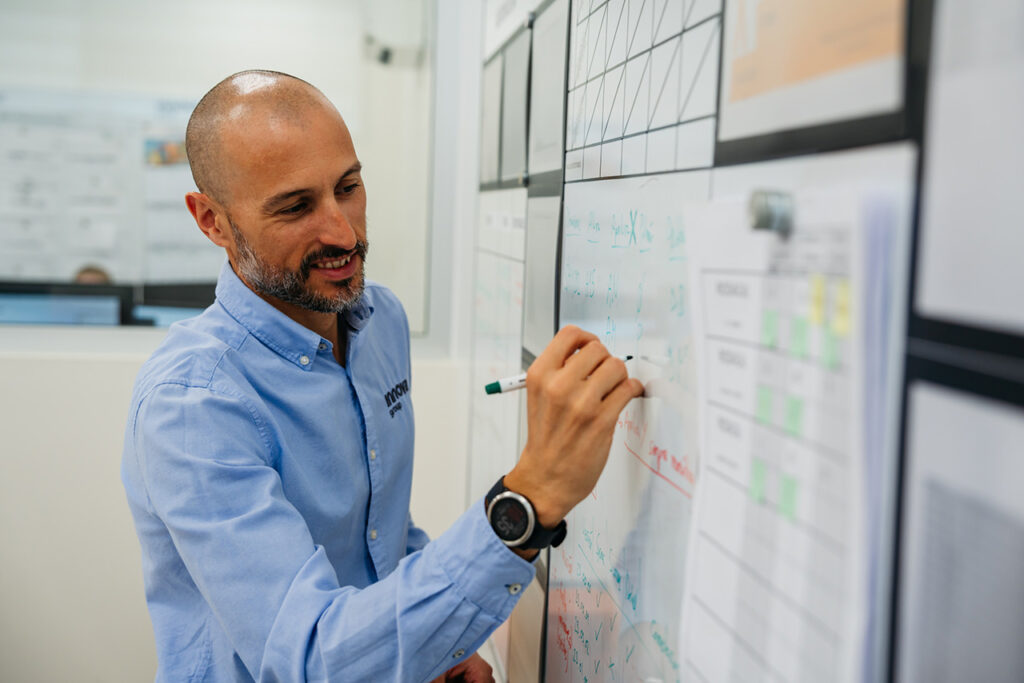
¿Cuáles serían las tareas típicas de mantenimiento de maquinaria de embalaje?
Dentro del mantenimiento preventivo de sistemas y líneas de embalaje, es importante realizar una serie de tareas esenciales, tales como:
- Limpieza: Eliminación de suciedad, polvo y residuos de los equipos para prevenir la acumulación que pueda causar corrosión u otros problemas.
- Lubricación: Aplicación de lubricantes a las partes móviles para reducir la fricción y el desgaste, y prevenir la oxidación y la corrosión.
- Ajustes mecánicos: Ajustes de componentesy conexiones sueltas para evitar que los equipos vibren y se desajusten.
- Inspección: Revisión de los equipos en busca de señales de desgaste, como grietas, fugas u otros daños.
- Calibración: Asegurarse de que cada componente de los equipos estén calibrados según las especificaciones del fabricante (ejemplo de rodamientos, motores, servos, etc).
- Reemplazo de piezas: Obviamente, cambio de piezas desgastadas o dañadas antes de que produzcan fallos en el equipo.
- Actualización del software de Control (PLC): Las actualizaciones del PLC por parte del fabricante pueden incluir novedades, parches de seguridad, mejoras en la interfaz de usuario, y optimizaciones en la eficiencia operativa.
- Verificación los sistemas de seguridad: Es importante también revisar regularmente los sistemas de seguridad, como los interruptores de emergencia, barreras de luz, y sistemas de parada automática para garantizar la seguridad del personal y evitar daños en los equipos durante su operación.
- Control de calidad de consumibles y materiales: Utilizar materiales de embalaje de calidad y especificaciones adecuadas, como los films y fleje, es también importante esencial para garantizar el buen funcionamiento de las máquinas de embalaje. Un material de baja calidad puede causar atascos, desgaste prematuro, o incluso daños en la maquinaria.
- Mantenimiento de los sistemas de transporte: Las transportadores no forman parte del equipo en sí pero es importante realizar inspecciones visuales periódicas en busca de desgastes, cortes o desalineaciones, además de la lubricación habitual, que pueden afectar la eficiencia del sistema y causar paradas no planificadas. Mantener los sistemas de transporte limpios y libres de acumulación de residuos también es vital para su buen funcionamiento.
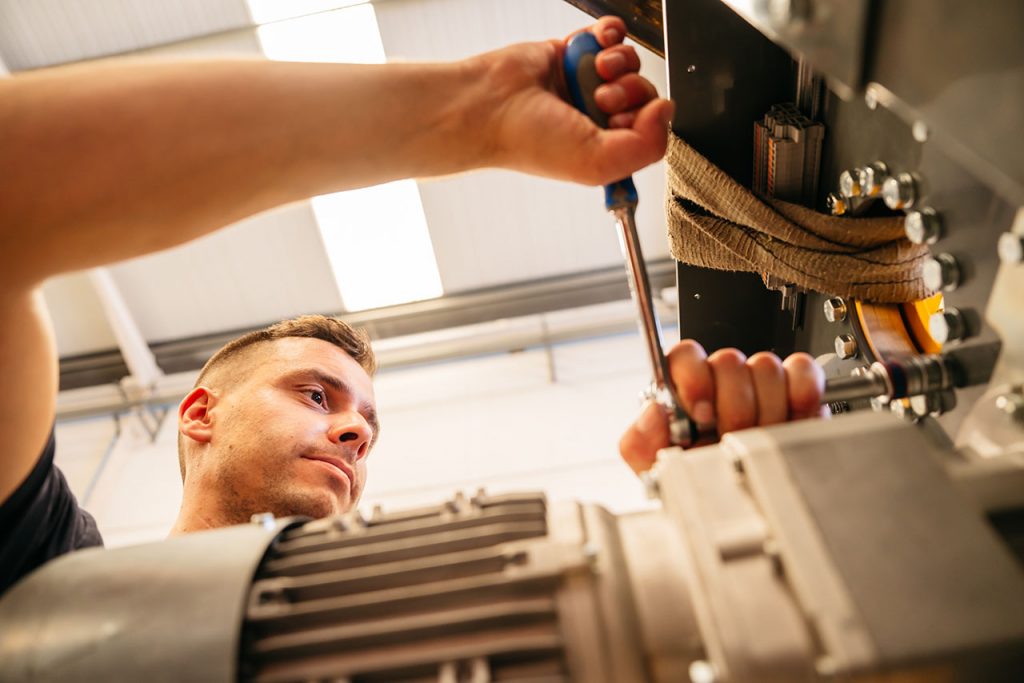
En definitiva es importante confiar en el fabricante para realizar el mantenimiento de nuestra maquinaria de embalaje, pero también conocer no solo el mantenimiento básico de limpieza y lubricación que debemos llevar a cabo en los equipos, sino todas las tareas mantenimiento que el fabricante puede llevar a cabo.
En Innova Maquinaria, entendemos que un buen mantenimiento preventivo es clave para mantener los sistemas de embalaje operativos y productivos al máximo nivel. Como fabricantes con más de dos décadas de experiencia, ofrecemos asesoría personalizada para garantizar que tu maquinaria funcione «como el primer día». Contáctanos sin compromiso para diseñar un plan de mantenimiento adecuado a tus necesidades.
>> ¿Te gustan nuestros posts técnicos de embalaje? Suscríbete a nuestra Newsletter mensual sobre consejos, actualidades y tendencias del sector logístico y embalaje.
SUSCRÍBETE: